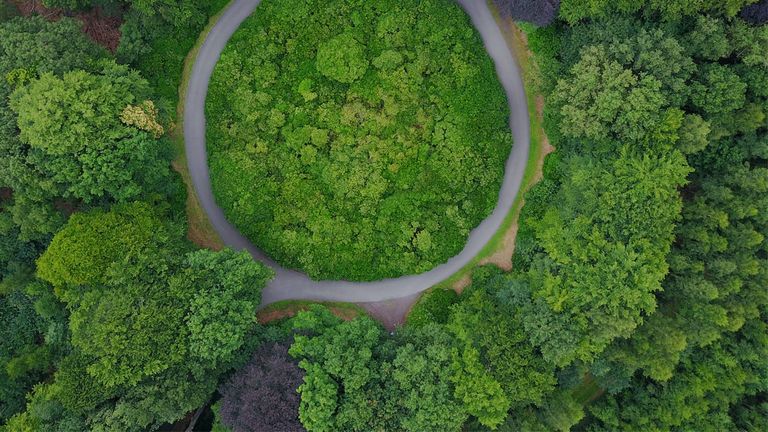
The severity of the current climate crisis demands global CO2 emissions be cut by 50 per cent within the next nine years. Technologies and business models based on a circular economy can make a significant contribution to this effort. Finding successful solutions will be invaluable for people, give businesses a competitive advantage and regenerative for our world.
The circular economy uses strategies such as innovative design, renewing, upgrading and recycling to eliminate waste throughout the value chain. The aim is to maintain the value of products, components and materials for as long as possible, reducing both the consumption of resources and greenhouse gas emissions. By adopting this approach, China reduced its CO2 emissions by 2.6 billion tons in 2020.
Circularity in practice
A circular mindset is quite a departure from the traditional linear value-creation model. Historically, raw materials have been used inefficiently because the initial focus was never on conservation. That meant they were processed into products that ended up in landfill, while in a circular economy they can be reused. Although circularity can mean different things in various industries, the principles remain the same: design out waste and pollution, keep products and materials in use, and recycle them at the end of their life.
Forward-thinking companies are building circularity into their sustainability strategies. The challenge is to provide customer solutions that help preserve the earth’s natural resources while contributing to an economically vibrant, low-carbon society. Companies that strike this balance will reap the benefits by unlocking new opportunities while creating a new generation of innovative resource-efficient businesses.
As a part of ABB’s 2030 sustainability strategy, our target is for 80 per cent of our products and solutions to be covered by a circularity approach. We have developed a framework to actively enable a circular economy, implementing it across our value chain and the lifecycle of our products and solutions.
This approach starts by considering the entire product lifecycle at the design and sourcing stage. Our goal is to develop products and solutions that can be produced in a resource-efficient manner that minimises the use of virgin or hazardous materials. As an example, we have developed IE5 ultra-premium efficiency motors that avoid the use of unsustainable rare-earth materials while achieving up to 40 per cent reduction in energy consumption.
Achieving total circularity is necessarily a gradual process. But strides are being made. ABB, for example, has implemented more than 40 recycling and waste reduction projects in 2021. Today, more than 40 per cent of our 447 sites around the world are already sending no waste to landfills. The target is for zero waste from our own operations to be disposed of in landfills, wherever this is compatible with local conditions and regulations.
Optimised use phase
Circularity is about more than just materials – it also requires consideration of other resources such as electricity. Motors in buildings and industrial applications account for nearly 45 per cent of today’s global electricity consumption. It’s been estimated that if all of the more than 300 million industrial electric motor-driven systems in operation were replaced with optimised, high-efficiency equipment, global electricity consumption could be reduced by up to 10 per cent. It’s clear that energy efficiency is a critical aspect of sustainability.
Smarter ways of recycling
Effective recycling is another important aspect of the circular economy because it ensures that materials stay within that economy as long as possible. An example of both principles in practice is ABB’s collaboration with a recycling company, and a Swedish pulp and paper company.
The company determined that it could reduce power use by upgrading a facility’s motors but had concerns about generating waste. By recycling the old electric motors and replacing them with more modern, efficient versions, the company was able to minimise waste while gaining all the benefits of the latest technology.
The process began with data gathering, as experts collected detailed information about the condition of the motors. Inefficient motors were removed and sent for recycling. The recycled metals – aluminum, copper, and iron – were then used to manufacture new, energy-efficient motors.
To date, 11 tonnes of obsolete motors have found their way to recycling, reducing CO2 emissions by almost 34 tonnes. In addition, 326 megawatt-hours (MWh) of energy and more than 100,000 cubic metres of water were saved compared with mining new metals. Today, 98 per cent of ABB’s motors are made from recycled materials, and circularity is a central consideration in the design process.
ABB has been developing, manufacturing and servicing electric motors and associated drive technology for more than 130 years, pushing the boundaries of energy efficiency. Now we are shifting the boundaries again by moving towards increasing circularity.
To learn more please watch the video: ABB Drivers of Progress: Episode 7 – Circular Economy
By Stefan Floeck, Division President IEC LV Motor Division, ABB Motion